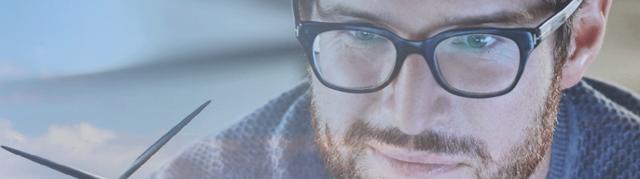
How to Increase Your Wind Farm’s Operational Reliability
Discover three key monitoring practices to increase your wind farm’s operational reliability, reducing downtime and maintenance costs.
Ensuring operational reliability in wind farms requires meticulous condition monitoring of turbine components. Effective condition monitoring can prevent unplanned maintenance and unexpected turbine downtime while enabling informed decisions on maintenance, service contract negotiations, end-of-warranty assessments, and lifetime extensions. Selecting a powerful condition monitoring solution, such as TCM®, gives you the necessary insights for these decisions.
Below are three crucial condition monitoring practices to enhance operational decision-making and improve wind farm reliability. These practices help lower operating expenses and contribute to a reduced Levelised Cost of Energy (LCoE).
Set alarm thresholds and monitor - even without kinematic data
Understanding the health of core components in the drivetrain can be challenging, particularly when acquiring or taking over a wind farm post-OEM warranty. A shift to condition-based monitoring and a predictive maintenance strategy can provide a fuller overview through detailed monitoring of changes in vibrational behaviour.
Retaining a detailed overview of changes to vibrational behaviour is crucial. It helps you understand whether vibrations deviate from the original operational mode. Ultimately, it’s about setting the correct alarms to react to changes in vibrations, preventing potential issues before they escalate.
If you’ve acquired older wind turbines, you might lack access to their kinematic data, which is crucial for identifying failure modes of mechanical components. We recommend using a condition monitoring system that works without kinematic data and sets precise alarm thresholds by capturing current vibration fingerprints. This patented method enhances security in condition monitoring by enabling alarm threshold calculations across the entire frequency domain of your components’ vibration spectrum.
Detect fault patterns and flag anomalous vibrations
A typical corrective maintenance approach may entail performing yearly or half-yearly wind turbine service inspections; however, faults in the drivetrain can rapidly develop between these intervals. Online condition monitoring becomes essential in such cases.
Various fault modes and patterns emerging under different operational and environmental conditions can be challenging to identify. However, a robust condition monitoring system makes this task more manageable by tracking and flagging unusual vibrational behaviours indicative of potential faults.
For instance, increased vibrations might be related to blade pass frequencies due to incorrect pitch offset settings left by a service team. Even though this might not cause immediate component failure, it can still lead to midterm overloads on other drivetrain components, ultimately affecting energy production.
Flagging unusual vibrations is critical for effective condition monitoring. Anomalies detected around one component, such as the main bearing, could stem from another, such as a nearby pump. By cross-referencing these findings with service logs, you can pinpoint the root cause and prevent cascading failures.
Apply fault prognosis and reduce spare part costs
Optimising maintenance operations is critical for ensuring the timely replacement of components before they disrupt energy production. This involves ordering spare parts and scheduling maintenance in advance. The cost implications are substantial, particularly for offshore wind farms, where initial equipment, permits, and staffing expenses can exceed $10,000 even before maintenance starts.
Fault prognosis can substantially reduce operations & maintenance costs while providing detailed insights into the health of your wind turbine fleet.
A condition monitoring service equipped with prognostics goes beyond traditional reporting. By aggregating maintenance data and employing machine learning, these systems can predict the probability of maintenance needs and repairs for specific components.
This allows you to schedule maintenance based on the availability of spare parts and seasonal weather conditions, thereby optimising operational costs and turbine uptime. For instance, if a main bearing is expected to require replacement in February, during peak wind season, you could postpone the maintenance until April. By placing the turbine in curtailment mode until then, you can avoid potential adverse weather conditions.
Fast track:
- Deploy condition monitoring systems that use current vibration fingerprints to set alarm thresholds, especially for older turbines lacking kinematic data.
- Regularly track and focus on unusual vibrations to detect potential faults early and prevent cascading failures.
- Leverage prognostic tools in monitoring systems to predict maintenance needs, reduce costs, and schedule repairs to optimise turbine performance and uptime.
Select a condition monitoring service provider
Due to scale, building an in-house monitoring team can be inefficient for small to midsize operators. Partnering with an external condition monitoring service provides expertise on various turbine models and eliminates hiring and training costs, enhancing your wind farm’s operational reliability and profitability.
At KK Wind Solutions, we leverage over 25 years of expertise in developing condition monitoring solutions specifically for the wind industry. Our flagship product, Turbine Condition Monitoring (TCM®), empowers wind farm owners and operators to predict turbine health and accurately inform operational decisions.
Our TCM® monitoring service detects early damage and faults across your wind turbine fleet and offers actionable recommendations. We set accurate alarm thresholds using a patented approach regardless of the availability of the turbine brand or kinematic data. With over 15 years of experience, our service delivers precise fault prognoses, enhancing operational decisions, reducing downtime, and increasing power production.
Best-in-class condition monitoring
Learn more about our monitoring service
Discover how you can reduce downtime and maintenance costs with TCM® Monitoring.