Avoid turbine failures and increase power production
Preventing wind turbine failures and understanding the health state of core wind turbine parts are essential commercial drivers when managing a wind farm.
With 25+ years of experience, TCM® is a state-of-the-art, secure wind turbine monitoring solution incorporating advanced vibration monitoring technology to identify emerging faults and damages in core wind turbine components.
TCM® empowers owners and operators to adopt a predictive maintenance strategy, improving operational decisions that help reduce turbine downtime and increase power production – providing site managers and maintenance personnel peace of mind.
Our solutions
TCM® enable you to detect emerging faults, anticipate spare part requirements, and precisely schedule maintenance, minimising downtime to the bare minimum.
A global leader in condition monitoring
25+
years of CMS experience
in the wind industry
75%
of all offshore wind turbines
operate with TCM®
30,000+
wind turbines across 40
countries operate with TCM®
END-TO-END CONDITION MONITORING
Predict failures and reduce maintenance costs
Our high-quality vibration sensors are designed to measure every vibration with high precision, whether vibrations occur in the main bearing, gearbox and generator or undesired tower sway, rotor imbalance or tail wag.
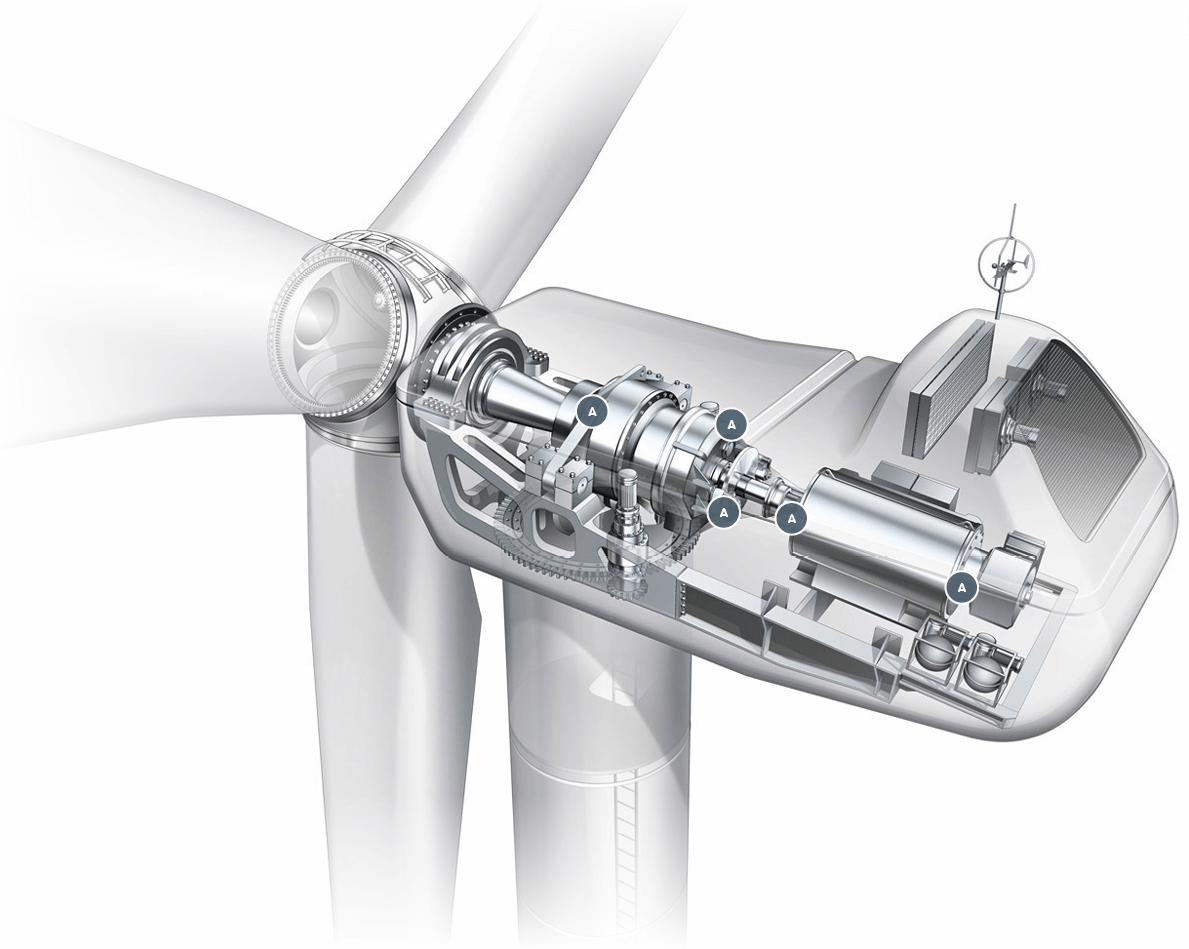
Accelerometers (A)
Mounted in the most important locations of the drive train, the accelerometers accurately monitor low frequency vibrations
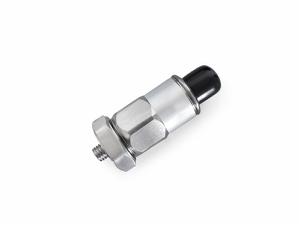
M-Sensors
The M-Sensors consists of two axial DC-coupled accelerometers, which monitor the tower sway and rotor imbalance.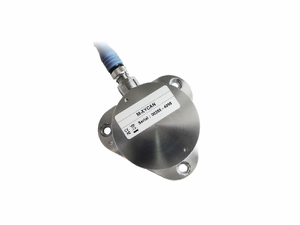
M-System
The M-system unit is placed inside the nacelle of the wind turbine. It collects data from all connected sensors simultaneously, processes information and transfers the data and alarms to your TCM® solution in the cloud.
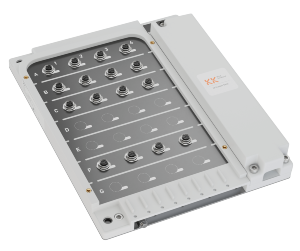
Data collection
TCM® collects data from other components, including RPM, Active Power and much more, providing you with the comprehensive view of your wind turbine's health.Mounted in the most important locations of the drive train, the accelerometers accurately monitor low frequency vibrations
The M-system unit is placed inside the nacelle of the wind turbine. It collects data from all connected sensors simultaneously, processes information and transfers the data and alarms to your TCM® solution in the cloud.
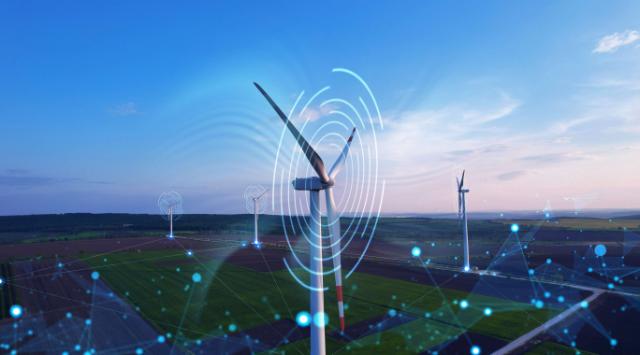
Cyber-secure and compliant solution
TCM® is built on a robust security foundation to protect IT and OT infrastructures against cyber-attacks and interruptions in energy production. Amid increased cyber threats, our solution is evolving to help you meet the new IEC62443 and NIS2 requirements, ensuring a clear path to compliance.
Deployment flexibility
TCM® integrates with your existing infrastructure, offering deployment options that meet your business’s IT needs while complying with your security and network standards.
Seamless integration with your IT systems
Enhance your wind turbine monitoring capabilities by seamlessly integrating TCM® with your SCADA, ERP, and other IT systems, allowing you to manage big data operations or undertake extensive data projects efficiently.
They trust us
Trusted by the world's leading wind turbine OEM's, Owners and Operators
Powerful and customisable diagnostics tool
A key feature of TCM® is the embedded diagnostics tool, Ocular, which enhances wind turbine monitoring by helping you diagnose and predict maintenance for essential wind turbine components.
Powerful diagnostics that improve your O&M
Our diagnostics tool provides you with a powerful analysis engine ideal for data mining, machine modelling, and much more. It supports the accuracy of your monitoring and maintenance workflows. Processing vibration monitoring data from your wind turbine fleet unlocks endless possibilities for implementing predictive maintenance.
Features include:
- Robust data-mining and visualisation platform.
- Integration of drivetrain models and kinematic data for comprehensive insights.
- Easy identification of fault signatures.
- Creation of measurement configurations, alarm setup, and much more.
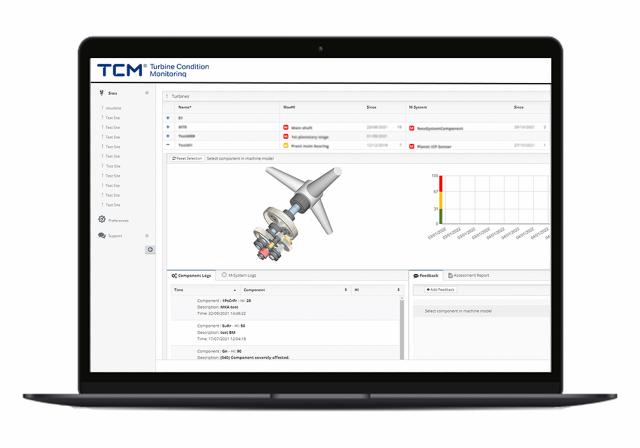
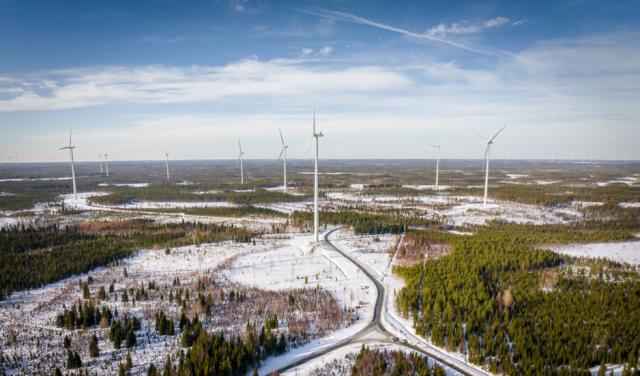
Case story:
Suomen Hyötytuuli optimises operations
Streamlining operations with unified data & analysis
The Finnish renewable energy production company, Suomen Hyötytuuli, faced challenges with wind turbines equipped with different Condition Monitoring Systems (CMS). This resulted in data from multiple CMS sources without a centralised platform to consolidate and analyse the overwhelming amount of information.
By connecting various CMS data sources to TCM®, the company established a unified platform for managing all wind turbine condition monitoring data. This integration provided comprehensive control over data and streamlined operations, making wind farm monitoring and maintenance more effective.
Expert monitoring for optimal performance
A reliable condition monitoring service helps you avoid unplanned downtime
Our TCM® Monitoring service detects early damages and failures, enabling predictive maintenance and helping you optimise O&M planning and spare parts sourcing, ultimately reducing downtime and maintenance costs.
Receive expert data analysis & insights
With TCM® Monitoring, our expert vibration data specialists provide premium insights that pinpoint the exact component issues, eliminating your need for in-house monitoring expertise.
Our team accurately identifies component issues and the health status of your wind turbine fleet through our proven condition based monitoring methodology, ensuring you avoid unnecessary maintenance visits and giving you peace of mind.
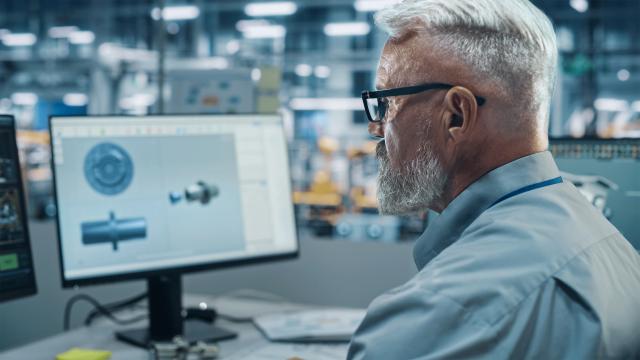
Experience TCM®
Get a free product demo
Discover how TCM® can help you avoid wind turbine failures, reduce downtime and save time and money on your operations & maintenance.